How to Do a DTF Transfer for Better Printing?
- Share
- Issue Time
- Apr 21,2023
Summary
In this blog post, we'll discuss everything from what DTF printing is and how it works to tips for making great transfers. Read on and learn how easy it is to make amazing DTF transfers.
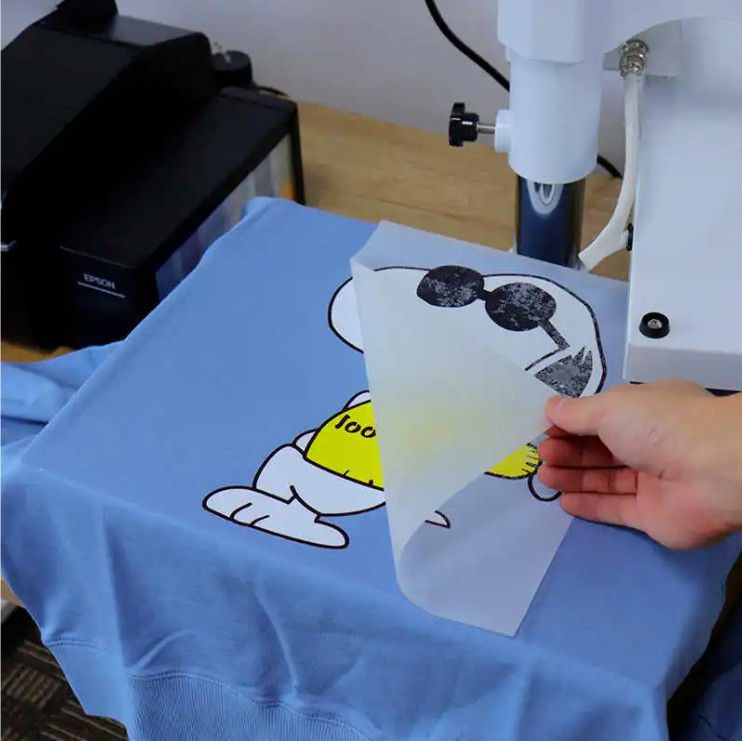
DTF printers provide users with an innovative and convenient method of image transfer. In traditional screen printing, you use a mesh to transfer the pattern onto the fabric, which is expensive and time-consuming.
With direct-to-film printing, PET film is available to DIYers and hobbyists. These films are approximately 0.75mm thick for better image transfer across the fabric. It also helps to make these materials into slices for home use and rolls for commercial use. In addition, PET films are available in both cold-peel and hot-peel types.
In this blog post, we'll discuss everything from what DTF printing is and how it works to tips for making great transfers. Read on and learn how easy it is to make amazing DTF transfers.
What Does DTF Need?
In this method of printing, your number one supply is DTF film transfer paper.
This direct-to-film printer can print on a specific film, usually a PET type. The PET film used in DTF printing is different from that used in screen printing. Since these films are approximately 0.75 mm thick, they are able to more accurately transfer small details in designs.
Additionally, you can find them as single sheets for individual projects or as rolls for commercial settings. Additionally, PET films are available in two temperature classifications – cold-peel and hot-peel. The device could start at under $1,000.
Software
For DTF (Direct to Film) printing, dedicated RIP (Raster Imaging Processor) software is essential. The software not only determines printing performance but also takes care of configuring colors. The software helps you manage ink volume and drop size, and other essential steps for optimal print quality.
Choosing the right software for your particular type of printer is critical. With the right software, you can get better results and change white and CMYK colors as needed. Unfortunately, most DTF printers don't have built-in RIP software but can support it. So make sure to choose the best option.
Hot melt powder is a white powdery adhesive, It has the characteristics of water resistance, good fastness, fast drying speed, not easy to block the net, and does not affect the color of the ink. It is a new type of environmentally friendly material. Hot melt is divided into coarse powder: 80 mesh, medium powder: 160 mesh, fine powder: 200 mesh, and 250 mesh.
You can print on DTF transfer paper with special inks of superior quality to meet a wide range of printing needs. The inks used are carefully crafted exclusive pigments in five colors (cyan, yellow, magenta, white, and black). White is the base layer. The machine will print the design with colored pigments on a white layer. It ensures that the colors are as vibrant as imagined. A bottle of ink can start at $80.
Curing Ovens and Heat Presses
A curing oven is a small industrial machine used to melt DTF powder onto a transfer film for transfer to any surface or fabric. Another option is to use a heat press, but some DIYers encourage curing in the non-contact mode for the best results. A curing machine can cost upwards of $450.
You will then need a heat press to transfer the DTF film to almost any fabric or surface. To produce high-quality prints with the least amount of hassle, it becomes essential to have an efficient and reliable curing oven or heat press.
Procedure for DTF transfer
So, how does direct transfer work? In this section, we will discuss the printing process using a special inkjet printer.
Create and Print Your Designs
The right RIP software can make or break your design. So make sure your software offers high-quality tools for efficient color profiling and an intuitive interface for quickly configuring these settings. With the right software, you can perform color profiling.
After printing an image in CMYK on PET film, you need to print white over the entire image. White is printed behind the actual image for successful results. Depending on the result you want, different types of PET films are available, such as glossy or matte, hot or cold peel.
When you want the fabric to look like the image you want, you have to prepare its mirror image before printing. The white ink is used as the base for the binder powder that will be used in the next step of the process. Taking care to follow these steps will ensure you get the highest quality results.
Chalking and Curing
Powdering is an integral step in creating high-quality DTF prints. It involves the application of hot-melt powder on a film with a printed image. While different printers may use different grades of powder, from small microns to large particles, DTF Print Transfer Specialists chose automatic powder vibrators to achieve an even amount of coating on the image. When done properly, this can greatly improve the compatibility, feel, and overall durability of printed fabrics.
Once the powder has been properly applied, the next step is curing. During this step, a curing oven melts the powder to help it adhere to the fabric or other surface material. Curing can sometimes vary between devices.
Larger printer operations will often use a curing oven or dryer, while smaller setups may opt for a heat press. Regardless of the tool used, curing the transfer is an important part of the process to ensure it can be shipped and stacked properly. Cured transfers can withstand high temperatures during their application to clothing.
Hot Pressing
After the design is printed on the film and the powder is cured, the next step is to heat press the transfer onto the garment. The temperature range for the heat press is 300-350F, depending on the DTF transfer being used. This process may take 10-20 seconds. Low-temperature DTF transfers are also available for applications using medium pressure at 280-290F for 12 seconds. Also, you can remove the film immediately after heating.
You now know how to print your designs using the direct-to-film method. How does it compare to other printing methods? Which one is better?
DTF and Sublimation Printing
Direct-to-film printing and dye-sublimation printing are two different methods of creating custom apparel and accessories. Both offer businesses a budget-friendly way to create professional projects with a professional look. The main difference between the two is the dye used. Sublimation uses special ink that is transferred to the fabric, while the direct film uses a special film that can hold the ink.
Both require a heat press and have similar setup requirements and costs, but the results can be very different. Direct film printing offers longer-lasting designs due to heavier ink deposits, while sublimation offers more vibrant colors and better wash resistance. Depending on your needs, any of these options can give you high-quality results at an affordable price.
Tips and Tricks for the Best Results
Direct-to-film printing is a great way to quickly produce vibrant, rich prints without the hassle of handling inks, paints, or plates. There are some tips and tricks to help you get the most out of your direct-to-film printing requirements.
First, make sure you're shooting at a high enough resolution. Otherwise, pixelation may appear when zoomed in. Second, pay attention to printer settings such as toner darkness and blade angle for the best color, clarity, and quality.
Second, always use high-quality glossy photo paper or mylar if you want impressive results.
Finally, do a test print on a small sample before going to a production print - you can verify if saturation needs tweaking, or if other corrections are needed before going to a large-scale print.
In Conclusion
DTF printing is outperforming other application-specific printing methods. It does not require a preprocessing process, which is often required in other transfers.
Additionally, DTF transfer printing works by printing your design onto a film, which is dusted, cured, and then heat-pressed onto the fabric of your choice. The DTF process is very good, but a bit expensive due to the equipment and specialized RIP software.
Finally, it works on cotton fabrics, polyester, cotton blend t-shirts, and treated leather. If you are looking for consumables such as a DTF printer, DTF ink, and DTF film for DTF printing, please contact us.
FCOLOR is a professional custom inkjet printer and ink manufacturer. Fcolor brand products are deeply loved and recognized by overseas customers. Products include: DTF printer inks, ink cartridges, dye inks, pigment inks, sublimation inks, eco-solvent inks, film inks, inkjet printers, PVC/ID cards, card printers, label printers; sublimation/digital printing equipment and consumables; also Provide customized solutions for customers.
1. Product name : Mini oven
2. mini oven size : A4 A3 A3+ pet film
3. stock :YES
4. easy to handle
The motor for DTF continuous supply can stir the ink to prevent liquid ink from settling and protect the print head
PU Powder,Good Health is the Best.
This product has strong compatibility, good printing effect, high-quality materials, high transfer rate